Why is proper maintenance of a power thresher important?
Improper maintenance, wrong machine settings, or faulty operation of a power thresher can increase losses and fuel consumption, and potentially endanger the operator’s health.
Thresher maintenance
Check the thresher for wear and tear
Check pulley surfaces. Rough grooves, if nicked, must be smoothened with a fine file. Cracked pulleys should be replaced immediately. |
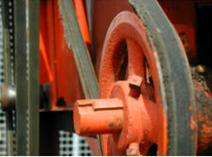 |
|
To prevent premature belt failure, check each belt’s alignment and tension. Adjust the idler pulley on the blower/cylinder belt to correct tension. |
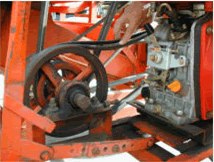 |
|
|
|
|
|
Check all pegs on the threshing cylinder for tightness. Loose pegs will damage the machine and may be dangerous to the operators. |
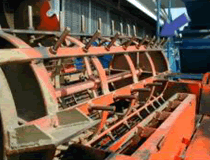 |
|
Examine the peg-teeth for wear. Worn pegs must be rotated 180 degrees or interchanged with those less worn. Badly worn pegs must be replaced or rebuilt by welding. |
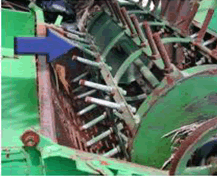 |
Make sure there are no loose or missing bolts and set screws. Tighten or replace as necessary.
Storage
- Clean the machine thoroughly.
- Remove belts and store these in a dry place.
- Paint parts that need repainting.
- Clean and apply oil to exposed metal surfaces in order to prevent rust.
- Store the machine in a clean, dry location and then cover it to reduce damage from dust accumulation.
- Follow the manufacturer’s recommendations on engine storage.
Lubricate
- Lubricate all bearings with good-quality, general purpose grease every 25 hours of operation.
- Periodically apply a small amount of oil to all hinge points.
- Check engine oil every day. Follow the engine manufacturer’s recommendations for oil change intervals and oil grade. Be sure the recommended oil level is maintained.
- Service the air cleaner, fuel filter, fuel line, carburetor, and spark plug regularly according to the engine manufacturer’s instructions.
Important machine settings
For peg-tooth drums the drum tip speed should be about 12−16 m/s. Choose higher speed for better threshing action, lower speed for less grain damage. The drum speed in revolutions per minute depends on the drum diameter (see table below).
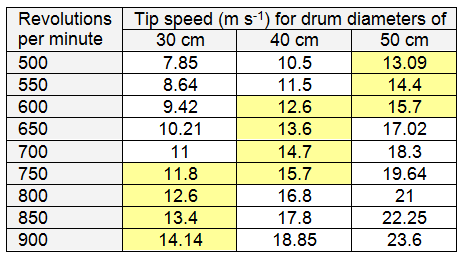 |
Clearances between peg-teeth and concave should be about 25 mm. A smaller clearance increases grain damage and might lead to clogging. Larger clearances reduce threshing efficiency.
|
|
For more information:
Visit the Rice Knowledge Bank website (http://www.knowledgebank.irri.org), email postharvest@irri.org; or call +63 2 580 5600.
Prepared by M Gummert with inputs from JF Rickman (2004); updated by M Gummert (2010)