Importance of drying the paddy correctly
Rice is usually harvested at grain moisture content (MC) between 24 and 26% (wet basis). Any delays in drying, incomplete drying, or uneven drying will result in qualitative and quantitative losses during:
- Yellowing or discoloration caused by mold development and heat build-up from respiration.
- Reduced milling yields caused by high temperatures and re-wetting of grains.
- Loss of germination and vigor from grain respiration, mold and insect activities, or from exposure to grains to temperatures above 42ºC.
- Damage caused by insects that are more active at higher MC levels.
Some recommendations on drying the paddy
- Clean the grains before drying to avoid uneven drying and wet spots.
- Dry the paddy immediately after harvest; use the 18% MC if the paddy will be stored for a maximum of two weeks.
- When drying for milling, maintain the MC to 14% so the grain weight and milling yield won’t decrease.
- When storing grains from 8−12 months, dry the grains up to 13% MC or less.
- For long term storage (1 year or more, maintain MC to 9%).
- Do not mix grains maintained at different MCs to avoid cracking.
- Always monitor the grain temperature and MC to prevent the grains from being exposed to excess temperatures and over-drying.
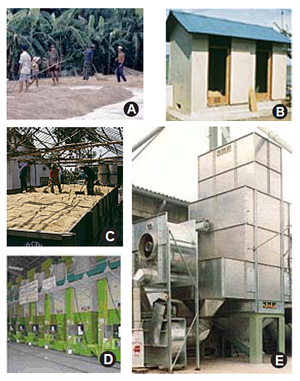
Methods of drying the paddy
A. Sundrying - Sun drying continues to be the preferred drying method in Asia because of its low cost. However, it is labor intensive and control of grain temperature is difficult.
For optimum quality:
- Spread the grains in thin layers (5 cm)
- Cover or collect the grains during rain
- Mix frequently, at least every 30 minutes
- Monitor the grain temperature
- Shade or cover when grain temperatures are above 50ºC (42ºC for seeds)
B. In-store drying - Paddy with MC below 18% can be slowly dried in storage bins using aeration with slightly pre-heated air (3−6K above ambient temperature).
Farm to commercial level, capacity depends on storage structure.
Drying time: days to weeks
- Pros: Good quality, low energy usage, storage included
- Cons: Second stage dryer, long drying time
Heated Air Drying
C. Fixed Bed Batch Dryer - for farmers, contractors, small rice mills. Capacity: 1−10 t/batch. Drying time: 6−8 h
- Pros: Simple, cheap, local versions available
- Cons: Uneven drying, labor intensive
D. Re-circulating Batch Dryer - for rice mills and cooperatives. Capacity: 4−10 t/batch. Drying time: 6−8 h.
- Pros: Even drying, automatic operation, affordable
- Cons: Wear of mechanical components
E. Continuous Flow Dryer - for large commercial facilities. Capacity: ~10 t/hour. Drying rate: 1−2% pass
- Pros: High capacity, automatic operation
- Cons: Capital intensive, requires large volumes
Prepared by M Gummert with input from JF Rickman (2004), updated by M Gummert (2011)